A partnership for energy innovation
The Additive Manufacturing Integrated Energy (AMIE) project is a research and design collaboration between SOM and the U.S. Department of Energy’s (DOE) Oak Ridge National Laboratory (ORNL). Highly energy efficient, the 3D-printed building was designed by SOM to produce and store renewable power and to share energy wirelessly with a 3D-printed vehicle, which was developed by the DOE.
The mobile power source combined with the structure’s highly energy-efficient design and rooftop renewable energy photovoltaics showcase possibilities for future off-the-grid human shelter. Innovative rapid prototyping took the project from concept to completion in less than one year, involving the University of Tennessee, Clayton Homes, General Electric, Alcoa, NanoPore and Tru-Design in addition to SOM.
AMIE is an outcome of the Governor’s Chair for Energy + Urbanism collaboration, a five-year research exploration in science and design involving ORNL, SOM, and the University of Tennessee’s College of Architecture and Design. This pioneering effort seeks to identify and develop innovative strategies for achieving a sustainable balance between the world’s rapidly growing cities, their energy demands, and the natural environment.
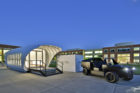